Home > Company News > Nitronic 60 (UNS S21800) Description
Company News
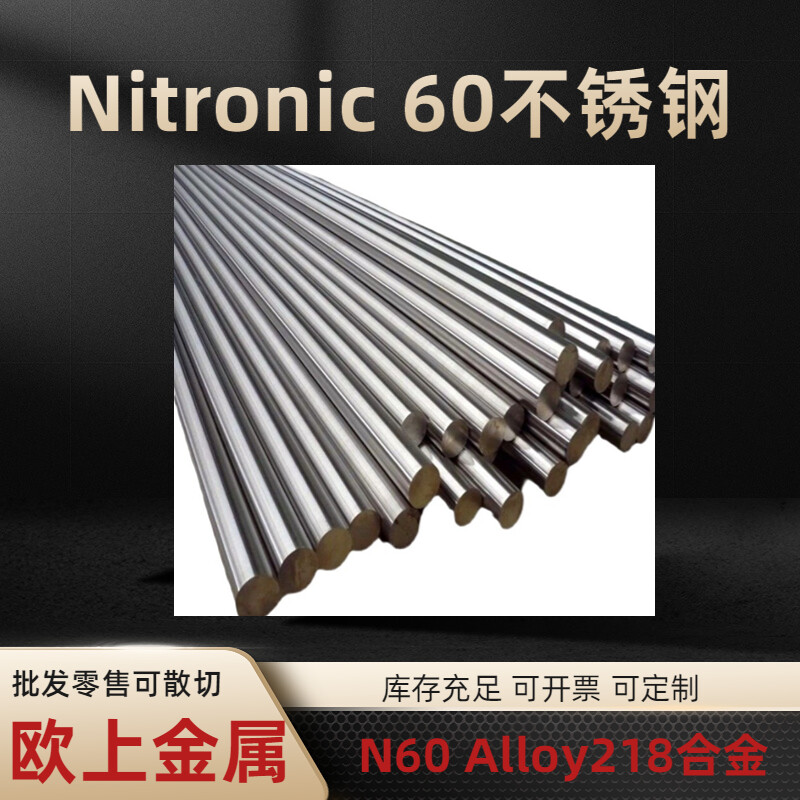
Nitronic 60 (UNS S21800) Description
The Nitronic 60 is known for its excellent wear resistance, even at high temperatures. Adding 4% silicon and 8% manganese inhibits wear, wear and tear. It is commonly used for a variety of fasteners and pins that require strength and wear resistance. It maintains good strength at temperatures up to 1800°F and has similar yang resistance to 309 stainless steel. General corrosion resistance between 304 and 316 stainless steel.
Chemical composition (wt %)
Carbon: ≤0.10 Silicon: 3.5-4.5
Chromium: 16.0-18.0 Phosphorus: ≤0.060
Nickel: 8.0-9.0 Sulfur: ≤0.030
Manganese: 7.0-9.0 Nitrogen: 0.08 ~ 0.18
Physical properties of Nitronic 60
Density, 3:0.275 pounds per inch
Modulus of elasticity, psi: 26.2 x 10 6
Coefficient of thermal expansion, 68-212˚F, /˚F: 8.8 x 10-6
Thermal conductivity, Btu/fthr˚F: 9
Specific heat, Btu /lb˚F: 0.12
Resistivity, Microhm-in: 28.7
Nitronic 60 Mechanical properties
Mechanical properties of annealed products as specified in ASTM A276
Yield strength (KSI) :≥50
Tensile strength (KSI) :≥95
Elongation (%) :≥35
Nitronic 60 parts are CNC processed differently from other Nitronic alloy parts because of the material's excellent resistance to wear (i.e. wear caused by local adhesion and subsequent tearing of material fragments when parts slide against each other). In addition to resistance to wear and tear, the Nitronic 60 has nearly twice the yield strength of more common stainless steels such as 316 or 18-8. Nitronic 60 also has far better corrosion resistance than most similar metals. These characteristics make it ideal for mechanical parts such as shafts, fasteners or gears that experience sliding contact and require high strength when subjected to corrosive operating environments.